آموزش کار با دستگاه تزریق پلاستیک
آشنایی گام به گام با فرآیند تزریق پلاستیک
در این مطلب از بسکو با فرآیند تزریق پلاستیک در ماشین های قالبگیری تزریقی آشنا خواهید شد. تزریق پلاستیک یک تکنولوژی ساخت برای تولید انبوه قطعات پلاستیکی یکسان با خطای پایین است. در این مطلب آشنایی گام به گام با فرآیند تزریق پلاستیک برای کاربران معمولی و تازه کار، هدف می باشد. البته لازمست با اجزای ماشین تزریق پلاستیک آشنا باشید، تا در ادامه بتوانید، که فرآیند تزریق پلاستیک را در انواع گوناگون آن دنبال نمایید.
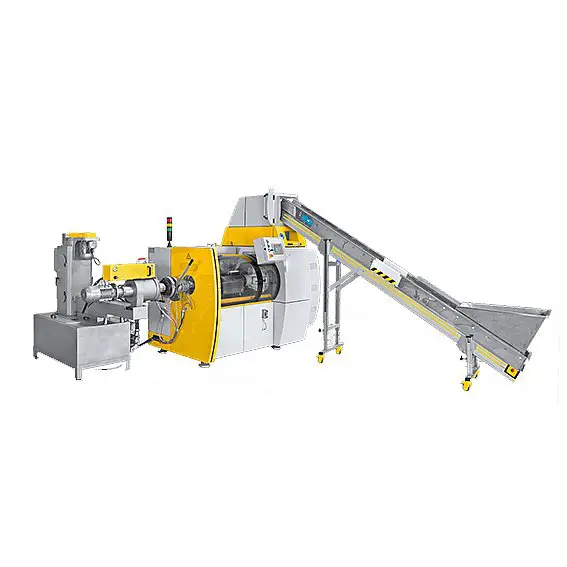
در تزریق پلاستیک ابتدا گرانول های پلیمر ذوب می شوند و سپس تحت فشار به درون یک قالب تزریق می شوند. پلاستیک مایع درون قالب خنک شده و جامد می شود. مواد اولیه تزریق پلاستیک پلیمرهای ترموپلاستیکی هستند که قابلیت رنگ آمیزی و پر شدن توسط افزودنی های دیگر را دارند.
تقریبا همه قطعات پلاستیکی که به طور روزمره از آنها استفاده می کنیم با استفاده از تکنولوژی تزریق پلاستیک ساخته شده اند: از قطعات خودرو و محفظه دستگاه های الکترونیکی گرفته تا لوازم آشپزخانه.
دلیل محبوبیت و استفاده گسترده از تزریق پلاستیک، هزینه بسیار پایین ساخت هر قطعه در تیراژهای بالا است. تزریق پلاستیک تکرار پذیری بالا را در کنار آزادی بالای طراحی ارایه می کند. محدودیت های اصلی تزریق پلاستیک از نوع اقتصادی هستند چون با اینکه تولید با استفاده از تزریق پلاستیک در تیراژ بالا بسیار به صرفه است، اما در مقابل سرمایه اولیه به نسبت بالایی برای شروع پروسه لازم است. از دیگر محدودیت های تزریق پلاستیک زمان نسبتا بالای رسیدن از طرح به تولید قطعه است(حداقل ۴ هفته).
در ابتدا می بینیم قطعات تزریق پلاستیک چگونه ساخته می شوند و تکنولوژی تزریق پلاستیک چگونه کار می کند. همچنین ویژگی های کلی این پروسه را که روی طراحی یک قطعه برای تزریق پلاستیک تاثیر دارند بررسی می کنیم. در ادامه به طور دقیق تر به مکانیک تکنولوژی تزریق پلاستیک وارد می شویم ، تاثیر این طرز کار روی هزینه های ساخت با این تکنولوژی را بررسی می کنیم و قابلیت های و محدودیت های کلیدی آن را بر می شماریم.
تزریق پلاستیک چگونه کار می کند؟
طرز کار تزریق پلاستیک:
۱.ابتدا گرانول های پلیمر خشک شده و در قیف قرار داده می شوند. این گرانول ها در قیف با پودرها و پیگمنت های رنگی و دیگر افزودنی های تقویت کننده ترکیب می شوند.
۲.گرانول ها به بشکه تغذیه وارد می شوند. گرانول ها در بشکه حرارت دیده،با یکدیگر ترکیب شده و با یک پیچ چرخان به سمت قالب هدایت می شوند. هندسه پیچ و بشکه به گونه ای بهینه طراحی شده است که به بالا بردن فشار به میزان لازم و ذوب شدن ماده کمک کند.
۳.تلمبه به جلو حرکت کرده و پلاستیک ذوب شده از طریق سیستم چرخنده به قالب تزریق می شود و همه فضای خالی قالب را پر می کند. با پایین آمدن دمای ترموپلاستیک، ماده جامد شده و شکل قالب را به خود می گیرد.
در نهایت قالب گشوده شده و قطعه جامد توسط پین های افشانک به بیرون هل داده می شود، سپس قالب دوباره بسته شده و پروسه برای تزریق قطعه بعدی تکرار می شود.
تکرار این پروسه می تواند بسیار سریع انجام شود: چرخه تزریق پلاستیک معمولا بسته به اندازه قطعه می تواند از ۳۰ تا ۹۰ ثانیه طول بکشد.
پس از آماده شدن محصول، قطعه روی کانوایر و یا در یک مخزن نگهدارنده رها می شود. معمولا قطعاتی که با تزریق پلاستیک ساخته می شوند به محض ساخت آماده استفاده بوده و نیازی به طی مراحل پولیش ، پرداخت و پست پروسس ندارند.
قالب گیری تزریقی
یکی از رایج ترین و مهم ترین روشهای ساخت قطعات پلاستیکی، استفاده از ماشین تزریق است.
قالب گیری تزریقی بر فرآیند تولید محصولات پلاستیکی تزریقی – بر مبنای ترموپلاستیک و ترموستها – اطلاق میگردد مواد پس از وارد شدن به سیلندری داغ، میکس و سپس توسط مارپیچ به داخل کویتهی قالب، جایی که قطعهی قالب گیری شده در آن سرد و سخت میگردد، رانده میشود.
پس از طراحی یک قطعه توسط مهندس یا طراح صنعتی، قالب متناسب با قطعه توسط قالبساز ساخته میشود. قالبهای تزریق عموماً از فولاد یا آلومینیوم و طی ماشینکاریِ دقیقی ساخته شده تا منعکسکنندهی ویژگیهای قطعه طراحیشده باشند. قالبگیری تزریق به منظور تولید طیف وسیع محصولات از کوچکترین اشیاء تا بدنه کامل اتوموبیلها، مورد استفاده قرار میگیرد.
ماشینآلات تزریق
دستگاههای تزریق پلاستیک متشکل از قیف تغذیه، متهی مارپیچی تزریق و واحد حرارتی میباشند. قالبها در صفحات گیرهی دستگاه قفل شده و سپس پلاستیک از دهانه اسپرو به قالب داخل و قطعه تزریقی ایجاد میگردد.
دستگاههای تزریق بسته به میزان نیروی اعمالی صفحات گیرهی آنها به تناژهای مختلف تقسیمبندی میشوند. این نیرو، قالب را هنگام فرآیند تزریق ثابت و بیحرکت نگاه میدارد. تناژِ دستگاه میتواند محدودهای مابین ۵ تا ۶۰۰۰ تن را در بر گرفته و البته تناژهای بسیار بالا از کاربرد نسبتاً کمتری برخوردار میباشند. نیروی گیرهی موردنیاز توسط مساحت تصویرشدهی قطعه تعیین میگردد.
سپس، به ازای هر اینچمربع از این ناحیه تصویرشده، ضریبی مابین ۲ تا ۸ تن در آن ضرب شده و نیروی گیره موردنیاز حاصل میگردد. به عنوان قاعدهای کلی، ۴ یا ۵ تن بر اینچمربع عددی قابل قبول برای اکثریت قطعات تزریقی محسوب میشود. اگر پلاستیک مورد استفاده بسیار خشک باشد، به فشار تزریق بیشتری برای پر نمودن قالب نیاز خواهیم داشت و نتیجتاً نیروی گیره بالاتری نیز برای نگاه داشتن قالب مد نظر خواهد بود. همچنین، نیروی گیرهی مورد نیاز ممکن است به واسطهی نوع مواد مصرفی و ابعاد قطعه تعیین گردد: قطعات پلاستیکی بزرگتر نیروی گیرهی بیشتری را نیاز خواهند داشت.
سیکل فرآیند تولید
سیکل تولید در فرآیند تزریق پلاستیک بسیار کوتاه و معمولا در حدود ۲ ثانیه تا ۲ دقیقه به طول میانجامد. این فرآیند شامل مراحل زیر میباشد:
· بستن
پیش از تزریق مواد به داخل قالب، ابتدا دو نیمهی قالب میبایست توسط واحد گیره به یکدیگر قفل شوند. هر دو نیمهی قالب به دستگاه متصلاند ولی تنها یکی از آن دو میتواند از قابلیت حرکت برخوردار باشد. واحد گیره با اتکا به نیروی هیدرولیکی، دو نیمهی قالب را به یکدیگر فشرده و با اِعمال فشار کافی آنها را در طی روند تزریق ثابت و بیحرکت نگاه میدارد.
زمان مورد نیاز جهت بستن و فشردن دو نیمهی قالب بسته به دستگاه مورداستفاده متغیر است: دستگاههای بزرگ (آنهایی که از نیروی گیرهی بالاتری برخوردارند) زمان بیشتری نیاز خواهند داشت. این زمان را میتوان با توجه به زمان چرخهی بیبارِ دستگاه مورد ارزیابی قرار داد.
· تزریق
مواد پلاستیکی خام معمولا به شکل تکههای پلاستیک به دستگاه وارد و توسط واحد تزریق به سمت قالب رانده میشود. در حین این فرآیند، مواد به واسطه اِعمال حرارت و فشار ذوب و سریعا به داخل قالب تزریق وارد میگردد. تجمع فشار پشت مواد، تراکم هرچهبیشتر آن در فضای داخلی قالب را در پی خواهد داشت. مقدار مواد لازم جهت پر نمودن کامل فضای قالب اصطلاحا شات نامیده میشود. به دلیل جریان پیچیده و متغیر مواد در قالب، عموما محاسبه و تخمین زمان تزریق دشوار میباشد. با این حال، این زمان میتواند با لحاظ نمودن حجم شات موردنیاز، فشار و قدرت تزریق، مورد ارزیابی قرار گیرد.
· خنککاری
مواد مذاب درون قالب به محض تماس با سطح داخلی آن، حرارت خود را به تدریج از دست خواهد داد. همزمان با این خنکشدن، مواد شکل و حالت قطعه موردنظر را به خود خواهد گرفت. اگرچه، در این مدت ممکن است پدیدهی کوچکشدن قطعه نیز به قوع پیوندد. تجمع و جریان بیشتر مواد به قالب در مرحله تزریق، میتواند مقدار کوچکشدنِ قابل مشاهده را کاهش دهد. قالب تا پایان مدتزمان خنککاری به صورت قفل و بیحرکت باقی میماند. همچنین، زمان خنککاری با در نظر گرفتن خواص ترمودینامیک پلاستیک و نیز حداکثر ضخامت قطعه قابل تخمین خواهد بود.
· خروج قطعه
پس از گذشتن زمان کافی، قطعه سردشده میتواند توسط سیستم پرانِ تعبیه شده در نیمهی پشتی قالب، از درون آن خارج گردد. هنگامی که قالب باز میگردد، مکانیزمی خاص با اِعمال فشار برای بیرون راندن قطعه وارد عمل میشود. نیاز به این اِعمال فشار بدان جهت است که قطعه در حین سرد شدن کوچکتر و به هستهی اصلی قالب جذب میشود.
جهت تسهیل بیرون راندن قطعه، گاها پیش از عملیات تزریق، از اسپری کردن عنصری کمکی به فضای داخلی کویتهی قالب استفاده میگردد. زمان موردنیاز جهت باز شدن قالب و نیز بیرون راندن کامل قطعه میتواند از زمان چرخهی بیبارِ دستگاه تخمین زده شود. پس از بیرون راندن قطعه، قالب مجدداً قفل و برای تزریق شات بعدی آماده میگردد.
قالب گیری بادی
قالبگیری بادی یک فرایند تولید است که در تولید قطعات پلاستیکی توخالی مانند بطریهای پلاستیکی به کار میرود. قالبگیری بادی به سه صورت انجام میشود: قالبگیری بادی اکستروژن، قالبگیری بادی تزریقی، قالبگیری بادی تزریق کششی.
فرایند قالبگیری بادی با گرم کردن پلاستیک و ایجاد لقمه اولیه آغاز میشود، لقمه اولیه به صورت یه استوانه یک سر آزاد دارای رزوه است که هوا میتواند از آن عبور کند، سپس لقمه داخل قالب قرار میگیرد و باد در آن دمیده میشود، فشار باد پلاستیک را هل داده و به دیواره قالب میچسباند، پس از خنک شدن پلاستیک و سرد شدن آن قالب باز شده و قطعه خارج میشود. در دو روش دیگر لقمه از تزریق در قالب مخصوص ایجاد میشود در مرحله دمیده شدن روش آخر یعنی قالبگیری بادی تزریقی کششی یک میله لقمه گرم شده را میکشد و در همین حال هوا در آن دمیده می شود.
انواع قالب گیری بادی
۱. قالب گیری بادی اکستروژن
۲. قالب گیری بادی تزریقی
۳. قالب گیری بادی کشش تزریقی
قالب گیری بادی اکستروژن
در این روش پلاستیک ذوب شده و سپس به شکل لقمه اکسترود میشود سپس این لقمه به داخل قالب رفته و باد داخل آن با فشار دمیده میشود، پس از سرد شدن قالب باز شده و قطعه خارج میشود. این فرایند به دو صورت انجام میشود یکی پیوسته و یکی متناوب، در فرایند پیوسته گرانولهای پلاستیک به طور پیوسته اکسترود شده و لقمههای اولیه تولید میشود، سپس وارد قالب شده و در آنها هوا با فشار دمیده میشود.
در فرایند متناوب ابتدا رزوه بالای لقمه ایجاد شده سپس با تزریق لقمه ایجاد میشود و سپس در آن دمیده میشود. در قالبگیری پیوسته وزن لقمه باعث تغییر ضخامت آن میشود و یجاد ضخامت یکنواخت را دشوار میسازد، برای حل این مشکل با سیستمهای هیدرولیکی به سرعت لقمه را از قالب خارج میکنند تا اثر وزن بر روی ضخامت دیوارهها حداقل شود.
برای مثال بطریهای شیر، بطریهای شامپو و آب پاشها با این روش تولید میشوند.
مزیت این روش هزینه پایین ابزار آن، سرعت تولید بالا و قابلیت ایجاد قطعات پیچیده است.
معایب این روش محدود بودن به قطعات تو داخلی و استحکام پایین قطعات تولیدی است
قالب گیری بادی تزریقی
این روش برای تولید انبوه قطعات تو داخلی شیشهای و پلاستیکی به کار میرود. در این روش لقمه اولیه با تزریق درست شده و سپس باد داخل آن دمیده میشود، این روش کمتر از بقیه روشهای قالبگیری بادی استفاده میشود و بیشتر برای تولید ظروف یکبار مصرف داروها به کار میرود. به طور خلاصه این فرایند به ۳ بخش: تزریق، دمیدن، بیرون انداختن.
در این فرایند ابتدا گرانولهای پلیمر در اکسترودر ذوب شده سپس با یک نازل داخل یک قالب تزریق میشود و لقمه ایجاد میشود سپس این لقمه از قالب خارج شده و داخل قالبی دیگر قرار میگیرد تا باد در آن دمیده شود، پس از سرد شدن قالب باز شده و قطعه خارج میشود.
قطعه نهایی با توجه به اندازه خود میتواند از ۳ تا ۱۶ حفره داشته باشد. برای خارج کردن قطعه از قالب معمولاً از ۳ پین پران استفاده میشود.
مزایا: دقت بالا
معایب: بیشتر در تولید بطریهای کوچک استفاده میشود زیرا کنترل فرایند دمیدن در ابعاد بزرگ دشوار است، به علت کشیده شدن پلاستیک، قطعات تولید شده استحکام بالایی ندارد.
راهنمای استفاده و اشتباهات رایج در هنگام استفاده از دستگاه های تزریق پلاستیک
همیشه زمانی که قصد خرید دستگاه های تزریق پلاستیک و شروع به کار و ایجاد کارگاهی تولیدی با استفاده از آن ها را دارید؛ باید به یک سری نکات توجه کنید. عدم توجه و رعایت این نکات باعث ایجاد مشکل در طول زمان برای شما خواهد کرد.
در ادامه به تعدادی از رایج ترین اشتباهاتی که خریداران مرتکب می شوند اشاره می کنیم:
اولین اشتباه: دستگاه تزریق پلاستیک دست دومی میخرید که خراب است!
مهم ترین نکته برای خریدن یک دستگاه تزریق پلاستیک دست دوم استفاده از نظر یک کارشناس خبره برای تایید سلامت تمامی بخش های دستگاه است. خرید دستگاهی که در گذشته خرابی و تعمیرات زیادی را داشته است اشتباه بزرگی محسوب می شود.
نکاتی که در ادامه به آن ها اشاره می شود لازم است در هنگاه خرید ماشین های تزریق پلاستیک رعایت شود.
1- جک و گیره دستگاه را چک کنید:
اولین کاری که در هنگام خریدن ماشین های تزریق پلاستیک باید انجام دهید این است که از سلامت سیستم گیره دستگاه مطمئن شوید.
بوش های مابین بازوهای گیره نقاطی هستند که در زمان باز و بسته شدن بازوها و وارد شدن فشار جک به گیره بیشترین درگیری را دارند و در صورت سالم بودن آنها بخش مهمی از مسئله سلامت گیره دستگاه تضمین شده خواهد بود، اما بخش دیگر آن که مربوط به دو صفحه دو سمت گیره است، یکی صفحه ثابت که فشار گیره را در زمان بسته شدن گیره تحمل می کند و همان صفحه قابل تنظیم برای قرارگرفتن درست قالب شما روی دستگاه است و صفحه ی دوم همان صفحه ی متحرک که نیمه ی سمبه ی قالب به آن متصل می شود.
سلامت بوش های گیره را می شود با وارد آوردن فشار به جک گیره دستگاه در حالتی که گیره باز باشد به راحتی فهمید، اگر با جک با فشارو وارد شده تکان بخورد و کاملا سفت نباشد نشان دهنده ی معیوب بودن و فیکس نبودن بازوهای گیره است و همین لقی بسیار کمی که وجود دارد می تواند باعث ناقص بودن قطعه تولید شده شود و مانع از یکنواختی فشار وارد شده بر صفحه ی قالب بعد از بسته شدن گیره و در نتیجه پلیسه دادن و کامل پر نشدن قالب شود.
اما در مورد صفحه پشتی دستگاه، در تمامی دستگاه های تزریق پلاستیک یک لقی کمی در این صفحه باید وجود داشته باشد. این لقی بخاطر قفل و باز کردن گیره در زمان باز و بسته شدن می باشد و در صورت عدم وجود این لقی، دستگاه بعد از قفل شدن گیره و بسته شدن قالب دیگر باز نخواهد شد و باید تمام صفحه ی عقبی دستگاه را باز کنیم!
اما لقی بیش از حدر نشان دهنده ی آسیب دیدن بوش های نگه دارنده صفحه یا رزوه های روی میله ی نگه دارنده ی این صفحه می باشد. این لقی بیش از حد هم نتایجی مثل خراب بودن بوش های بازو ها را به شما میدهد؛ این ایراد در صورت وجود زمانی قابل رویت است که گیره در زمان بسته شدن تحت فشار باشد، یعنی قالب بر روی دستگاه بسته شده باشد.
اما آخرین مورد در حیطه بررسی گیره دستگاه، جک هیدرولیک گیره می باشد که باید از لحاظ خرابی احتمالی در زمان کار کردن دستگاه مورد بررسی قرار بگیرد، یک نشتی کوچک از خود جک یا سر شیلنگ ها می تواند سیستم گیره دستگاه را به حداقل راندمان کاری برساند، حتی اگر بوش ها و صفحه ی عقبی دستگاه سالم باشند.
2- سیستم تزریق را چک کنید:
مهمترین بخش از سیستم تزریق را سیلندر و ماردون آن تشکیل می دهند. کار کردن افراد ناشی با دستگاه و وارد آوردن فشارهای بالا برای رفع یک عیب کوچک و گشاد شدن قطر داخلی سیلندر دستگاه می تواند دستگاه را نا کارآمد کند، با گشاد شدن سیلندر قطعاتی که با پیچیدگی همراه هستند و برای تزریق کامل نیاز به فشار بالا دارند قطعا ناقص تزریق خواهند شد و عملاً پول و زمان زیادی از دست خواهد رفت، سلامت قسمت مهم دیگر یعنی ماردون با بارگیری کامل و تزریق کامل مقدار حجمی از مواد که دستگاه به آن حجم تزریق شناخته میشود مشخص خواهد شد، البته نه در شرایط آزاد، بلکه در شرایط تحت فشار تزریق که ماردون سلامت خود را نشان خواهد داد.
مشابه به بخیش گیره، بخش های دیگر دستگاه مانند: جک اصلی بخش تزریق و گرداننده هیدرولیکی ماردون و جک حرکت دهنده بخش تزریق نیز می بایست از لحاظ عدم نشتی مورد بررسی قرار بگیرد. مهمترین و البته ساده ترین بخش سیستم های تزریق، هیترها یا المنت های دستگاه می باشند که باید از سالم بودن آن ها نیز مطمئن شوید.
3- از سالم بودن الکترو موتور و بخش هیدرولیک دستگاه مطمئن شوید:
دستگاه را می بایست از لحاظ سالم بودن شیرهای برقی، سر شلنگ ها و بخصوص الکتروموتور بررسی نمود، نشتی داشتن شیرهای برقی می تواند کلاً فرایند تزریق را مختل کند، بعنوان مثال نشتی در شیر برقی بخش گرداننده ماردون در زمان ایست دستگاه و باز شدن قالب و آماده شدن دستگاه برای تزریق بعدی، در زمان گرم بودن مواد در سیلندر باعث گردش بدون فرمان ماردون و جلو آمدن مواد و بیرون ریختن از بوش قالب شده که بایستی در هر بار تزریق این مواد را پاک کرده و دوباره تزریق کنید که همین عمل بظاهر ساده می تواند باعث خنک شدن و تزریق ناقص قطعه گردد.
4- بخش فرمان دستگاه را چک کنید:
کنترل دستگاه چه از نوع کنتاکتوری باشد و چه پی ال سی، باید مورد استفاده و عمل قرار گیرد تا صحت عملکرد آن مشخص شود، همچنین کنترل سنسورهای حرارتی دستگاه در حین کار و فرمان به جک های هیدرولیک دستگاه باید بصورت کامل و بی عیب صورت گیرد.
دومین اشتباه: نوع موادی که برای کار با دستگاه استفاده می شود را مورد توجه قرار دهید.
اکثر مارپیچ ها می توانند با اکثر مواد پلاستیکی مانند PP، PE، ABS و PC استفاده شوند، بنابراین آنها بسیار انعطاف پذیر و مناسب برای شرکت های تولیدی هستند که انواع مواد مختلف را تزریق کنند. اما در مواقعی و در استفاده در بعضی مواد خاص نیاز به استفاده از مارپیچ با طراحی ویژه می باشد که در صورت عدم توجه به این مسئله، تولید کننده با مشکلاتی روبرو خواهد شد.
سومین اشتباه: محدودیت فشار تزریق و میزان فشار قفل را چک کنید:
توصیه می شود دستگاه انتخابی حداقل 10٪ ظرفیت فشار تزریق بیشتری داشته باشد تا در صورت تولید قطعه ای با وزن متناسب با دستگاه ولی با ضخامت کمتر ، عملکرد دستگاه با مشکل مواجه نشود. همچنین اگر ضخامت جنس تولیدی کم است بهتر است دستگاه یک سایز بزرگتر انتخاب شود تا بتوان با فشار قفل کمتر جنس را بدون مشکل ظاهری و کیفی تولید نمود.
چهارمین اشتباه: مطمئن شوید که از تناژ مناسب استفاده می کنید:
اگر تناژ دستگاه کم باشد، تولید قطعات با کیفیت مشکل خواهد بود. تناژ کم باعث وزن غیر ثابت در محصول تولیدی، ایجاد پلیسه، کوچک و بزرگ شدن محصول و کیفیت سطحی نامناسب می شود.
پنجمین اشتباه: انرژی کمتری مصرف کنید:
در نظر داشته باشید که اندازه قالب و قطعه ای تولیدی شما تاثیری در میزان مصرف انرژی نخواهد داشت.
در طول زمان، استفاده کردن از یک دستگاه تزریق با مصرف انرژی کمتر تاثیر چشم گیری در روند سود آوری شرکت شما خواهد گذاشت. از این رو می بایست با توجه به زمان های توقف در سیکل تولید ، انتخاب موتورهای سروو و یا پمپ دبی متغیر و نیز نصب اینورتر روی الکتروموتور مد نظر قرار گیرد.
با انتخاب درست در خرید دستگاه تزریق می توانید مدت زمان طولانی تری از دستگاه استفاده کرده و باعث افزایش راندمان دستگاه می شود.