اهن را چگونه از سنگ معدن جدا می کنند
آهن، فلزی است که ارزش و نقش حیاتی آن در تمامی بخشهای اقتصادی و اجتماعی بر کسی پوشیده نیست. به طوری که خود کفایی و پویا بودن یک کشور در استخراج آهن، موفقیت و پویایی صنایع وابسته را در پی خواهد داشت. به دست آوردن سنگ معدنی این فلز از اعماق معادن و تبدیل آن به قطعات مستحکمی که به صورت آلیاژهای مختلف در اتومبیلسازی، ساختمانسازی، پلسازی، کشتیسازی و… قابل استفاده باشند، مستلزم طی کردن فرآیندهای فیزیکی، شیمیایی و مکانیکی ویژهای است. در این مقاله، عملیات و مراحل مختلف استخراج آهن، از معدن تا کارخانه را مورد بررسی قرار داده و به جزئیات مهم آنها میپردازیم.
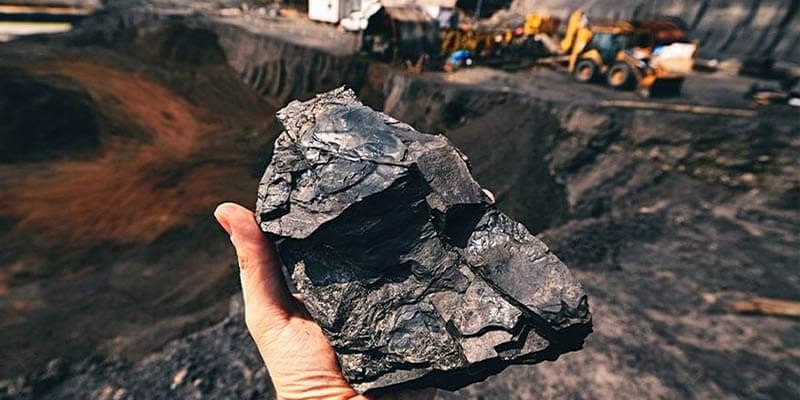
ورق St52 با توجه به کاربرد بالا در کشورمان، در ایران و در شهر اصفهان و اهواز تولید و عرضه میگردد.
سنگ آهن چیست و انواع آن
سنگ آهن (Iron ore) یکی از فراوانترین سنگهای معدنی در زمین است که تشکیل آن به تدریج و در طی سالهای طولانی صورت میگیرد. قیمت شمش آهن و دیگر محصولات نهایی به دست آمده، به ارزش سنگ آهن وابسته است. حدود ۵ درصد از پوسته کره زمین را اکسیدهای آهن تشکیل میدهند. علاوه براکسید، آهن به شکلهای ترکیبی دیگری مانند سولفوریا سولفید، کربنات، سیلیکات وآرسنیکی نیز یافت میشود. به طور کلی تمام سنگهای پوسته به استثنای برخی سنگهای آهکی، حاوی مقداری آهن در ترکیب خود هستند.
بالغ بر ۳۰۰ نوع کانی آهندار در طبیعت یافت میشود که نوع ترکیب و عیار (درصد آهن خالص موجود در سنگ آهن) آنها با یکدیگر متفاوت است و فقط تعداد معدودی از آنها که به طور کلی اکسیدهای آهن هستند، قابلیت تصفیه و جداسازی آهن موجود را دارند.
مگنتیت و هماتیت نسبت با سایر کانیها از اهمیت بیشتری برخوردار مگنتیت به علت خاصیت احیاپذیری کم، به صورت مستقیم کاربرد ندارد و باید تحت عملیات کلوخهسازی یا گندلهسازی قرار بگیرد تا شکل کانیشناسی آن عوض شود.
اولین قدم در جهت استخراج آهن، شناسایی معادن بالقوه آن و نوع کانیهای موجود در این معادن است. روشهای متعددی برای شناسایی این معادن وجود دارد، مانند:
- عکسبرداری هوایی
- برداشت زمینشناسی
- ژئوشیمی
- بیوژئوشیمی
- برداشت الکتریکی
- برداشت ژئوفیزیک
- حفر گمانه
معدن یا همان کانسار آهن میتواند نزدیک سطح (تا عمق ۱۰۰۰ متر) یا اعماق زمین (تا عمق ۲۰۰۰ متر) قرار داشته باشد. این عمق قرارگیری و همچنین شکل و عیار کانسار، در نحوهی استخراج آهن تاثیرگذار هستند. عیار ۷۰ درصد به عنوان یک عیار مطلوب و اقتصادی برای استخراج آهن در نظر گرفته میشود و در صورتی که مقدار عیار از ۶۰ درصد پایینتر باشد، استخراج سنگ آهن اقتصادی نخواهد بود.
مراحل استخراج سنگ آهن چیست؟
پس از شناسایی معدن، با توجه به خواص سنگ آهن مربوطه، روش استخراج این سنگهای معدنی تعیین میشود. برای این منظور میتوان از شیوههای ژئوفیزیکی مانند مغناطیسسنجی استفاده کرد. استخراج روباز (سطحی) و استخراج زیرزمینی دو روش اصلی برای استخراج سنگ آهن هستند که با توجه به عمق سنگ آهن، شکل آن و مسائل اقتصادی، میتوان آنها را به کار برد. استفاده از روشهای روباز در اکثر معادن دنیا متداولتر است.
به طور کلی این روشهای استخراج آهن (در حالت سنگ)، شامل چهار مرحله اصلی هستند:
- حفاری: به این منظور ابتدا چند چال با الگوی مشخص، توسط دستگاههای حفاری مخصوص ایجاد میشوند و درون این چالها با مواد منفجره پر میشود.
- انفجار: پس از تخلیه محل مورد انفجار و جمع شدن کارکنان در محل ایمن، عملیات انفجار برای خرد کردن سنگها آغاز میشود. پرکاربردترین مواد منفجره برای خرد کردن سنگ آهن، امولسیون و مخلوط نیترات آمونیوم و بنزین (آنفو) هستند.
- بارگیری: پس از خرد کردن سنگها، آنها را توسط تجهیزاتی مانند کامیون و شاول بارگیری میکنند. شاول، سنگهای خردشده را از روی زمین برداشته و درون کامیون میریزد. گنجایش این شاولها با توجه به مدلشان از 2 تا 10 متر مکعب متفاوت است.
- باربری: در این مرحله کامیونها یا اصطلاحا دامپتراکها، مواد را به کارخانه فرآوری منتقل میکنند. ظرفیت تراکها معمولا 100 تن است.
فرآوری سنگ آهن و مراحل ان چگونه است؟
سنگ آهن را نمیتوان به طور مستقیم استفاده کرد و لازم است ابتدا مواد با ارزش (ماده معدنی) را ازمواد بیارزش (باطله) جدا کرد که به این عمل فرآوری میگویند. متداولترین روش فرآوری سنگ آهن شامل شش مرحله غربالگری، خردایش، آسیاب کردن، جدایش ثقلی و جدایش مغناطیسی است.
- غربالگری: در اولین مرحله از فرآوری سنگ آهن، قبل از ریختن مواد در سنگشکن، قطعات کوچک به وسیله سرند جدا میشوند که به این عمل غربالگری گفته میشود. این کار باعث کاهش وزن خوراک سنگشکن و افزایش بهرهوری
- خردایش: پس از سرند کردن مواد، ذرات بزرگ را به سنگشکن انتقال میدهند. این سنگشکنها انواع مختلفی دارند که نوع فکی، ژیراتوری و مخروطی آن در این زمینه بیشتر استفاده میشوند. در این مرحله، خردایش یا خرد کردن سنگ آهن تا رسیدن به ابعادی حدود ۳۴۲ میکرون ادامه پیدا میکند. بعد از اتمام این کار، مواد خردشده را به محل دپوی مادهی معدنی منتقل میکنند.
- آسیاب کردن: پیش از انتقال مواد به مرحله جدایش ثقلی، آنها را وارد آسیاب میکنند. اگر آسیاب کردن مواد به درستی صورت بگیرد، انتقال مجدد به مرحله سرند و خردایش به حداقل رسیده و انرژی کمتری مصرف میشود. مواد بعد از خروج از آسیاب، توسط سیلیکون یا صفحه لرزان، به ذرات کوچک و بزرگ تقسیم میشوند. سپس ذرات بزرگ به مراحل قبلی بازگردانده میشوند.
- جدایش ثقلی: در این مرحله که دو تا سه بار تکرار میشود، ذرات سنگین به وسیله نیروی گریز از مرکز از ذرات سبک جدا میشوند. این عمل به کمک مارپیچهای مخصوص و آب صورت میگیرد. در انتهای این مارپیچها مخزنی وجود دارد که مواد سنگین را از سبک جدا کرده و در خود جمع میکند. به این مواد کنستانتره میگویند.
- جدایش مغناطیسی: کنستانتره به دست آمده در مراحل قبلی، سنگ آهن کمی دارد. برای افزایش عیار سنگ آهن، مواد جمعشده در مرحله جدایش ثقلی را به طور مستقیم به فرآیند جدایش انتقال میدهند تا به وسیله طبلکهای مغناطیسی جذب شوند. مواد سبک جداشده قبلی نیز برای جداسازی آهن، در کوره پخته میشوند.
آهن فرآوری شده پس از طی این مراحل، به صورت سنگ آهن دانهبندیشده، کنستانتره و گندله به کارخانه ذوب منتقل میشود تا آهن خالص به دست بیاید.
آهن خام چگونه تولید میشود؟
پس از انتقال مجموعه سنگ آهن کلوخه شده به کارخانه ذوب، فرآیند احیای آهن آغاز میشود. برای این کار، از دو روش کورهی بلند و قوس الکتریکی استفاده میشود.
روش کوره بلند: در این روش که بیش از ۹۰ درصد سنگ آهن استخراج شده در جهان به وسیله آن احیا میشود، سنگ آهن را همراه با آهک و کک، به صورت لایه لایه و از بالا وارد کوره میکنند. کک در این کورهها نقش تامینکننده انرژی را به عهده دارد و در دما ۳۰۰ درجه سانتیگراد، با دمش هوا و اکسیژن میسوزد و گرمای لازم برای ذوب سنگ آهن را فراهم میکند. با افزایش درجه حرارت و آزاد شدن گاز مونواکسید کربن در اثر احتراق ناقص کک، آهن احیا میشود. آهن خام تولیدشده با این روش، دارای ۳ تا ۴ درصد کربن و نقطه ذوب آن حدود ۱۳۰۰ درجه سانتیگراد است.
روش قوس الکتریکی: در مقایسه با کوره بلند، قدمت این روش بسیار کمتر است. این روش بر اساس استفاده از آهن اسفنجی و قراضه فولاد طراحی شده است. آهن اسفنجی که ساختاری متخلخل دارد، از احیای مستقیم اکسید آهن در کورههای احیای مستقیم به دست میآید. عیار آهن اسفنجی بالای ۹۲ درصد بوده و میزان کربن آن نیز ۷/۱ درصد است. در روش کوره قوس الکتریکی، آهن قراضه یا آهن اسفنجی را به همراه آهک، کک و بنتونیت، به کوره قوس وارد میکنند تا ناخالصیهای آن حذف شود. سپس آن را به عنوان ماده اولیه برای تولید شمش فولاد، به واحدهای ریختهگری ارسال میکنند؛ پس نتیجه می گیریم که قیمت آهن کیلویی و شمش آهن به روش تولید آن نیز بستگی دارد.
احیای مستقیم
برای تولید آهن اسفنجی مورد نیاز در کورههای الکتریکی، روشهای گوناگونی ابداع شده که مهمترین آنها، فناوری میدرکس است. روشی که اولین بار توسط شرکتی آمریکایی با همین نام، به کار گرفته شد. در حال حاضر ۶۳ درصد آهن اسفنجی جهان با این شیوه تولید میشود. شرکت مکزیکی HYL نیز اخیرا با حذف رفرمر گازی، از نسل چهارم کورههای خود رونمایی کرده است. از دیگر روشهای تولید آهن اسفنجی میتوان به DRC، Jindal، SL/RN و روش ایرانی PERED اشاره کرد. در روشهای احیای مستقیم، حذف تعدادی از مراحل آمادهسازی باعث کاهش هزینهها و آلودگیها شده است. این روشها در سه دهه اخیر به طور گستردهای توسعه پیدا کرده اند. استفاده از گاز طبیعی متان در این روشها باعث شده تا اجرای آنها در کشورهایی مانند ایران که سرشار از منابع گاز طبیعی هستند، بسیار سودآور باشد.
روش میدرکس: در این روش، همزمان با دمیده شدن گاز طبیعی به داخل، گندلهها از قسمت بالایی کوره به پایین سقوط میکنند. گاز طبیعی به دلیل جریان سیال داغ (دمای ۱۰۰۰ درجه سانتیگراد)، به سمت بالا حرکت کرده و باعث کاهش درصد اکسیژن گندلههای در حال سقوط میشود. به این ترتیب آهن اسفنجی به دست میآید.
مرکزآهن، متشکل از تیمی جوان و پویا، بزرگترین بازرگانی آهنآلات و دارای اولین ساختمان تخصصی و بهروز در زمینه خرید و فروش انواع مقاطع فولادی است
روش HYL: مانند روش میدرکس در این فرآیند هم از گاز طبیعی شکستهشده و همچنین بخار آب را برای تولید گاز احیایی هیدروژن به عنوان احیاکننده استفاده میشود. در این روش، میزان هیدروژن موجود در مخلوط گاز احیایی، نسبت به مونوکسید کربن بسیار بیشتر بوده و هیدروژن، نقش عامل احیاکننده اصلی را ایفا میکند.
هر دوی این فرآیندها، در کوره شافت عمودی انجام میشوند که توسط مکانیزمهای مکانیکی (هیدرولیکی)، آببندی شده و فشار محیط در آن بسیار بالا (تا ۷ اتمسفر) تنظیم شده تا سرعت موردنیاز برای واکنش احیای مستقیم تامین شود.
روش تولید فولاد از آهن خام
برای تولید فولاد از آهن خام مذاب، از تکنولوژی کورهی بلند-کنورتر یا همان بسمر استفاده میشود. آهن خام سه نوع دارد:
- آهن خام سفید: سرد کردن سریع آهن خام مذاب، از تشکیل گرافیت جلوگیری میکند. این آهن که جنس آن سخت و ترد است در فولادسازی کاربرد داشته و مقدار سیلیسیوم آن کم است.
- آهن خام خاکستری: سرد کردن آهسته آهن خام مذاب، باعث میشود که کربن به شکل گرافیت دربیاید. مقدار سیلیسیوم موجود در این آهن کم بوده و باعث تردی آن میشود.
- آهن خام نیمهخاکستری: خواص آن بین دو نیمهی قبلی بوده و در تولید فولاد و چدن کاربرد دارد. این آهن، مقاومت پایینی داشته و در برابر اکسید شدن و ضربه خوردن، آسیبپذیراست. به منظور تبدیل این ماده به فولاد مستحکم موردنیاز در صنایع، باید ترکیب عناصر موجود در آن تنظیم شود.
در این روش که به آن احیای غیرمستقیم نیز گفته میشود، آهن خام مذاب به دست آمده از فرآیند کوره بلند را درون کوره اکسیژنی میریزند و با دمش گاز اکسیژن خالص، کربن و ناخالصیهای اضافی آن را میسوزانند. در نتیجه کربن فولاد به مقدار موردنظر میرسد. سپس با افزودن عناصر آلیاژی، استحکام فولاد را افزایش میدهند. این تکنولوژی مهمترین شیوه تولید فولاد خام در جهان است که بیش از ۶۰ درصد از کل فولاد خام دنیا با استفاده از آن تولید میشود.
تولید فولاد با این فرآیند، از نظر نرخ تولید بازدهی بالایی دارد؛ اما نیازمند مواد خام باکیفیت است. یکی از این مواد اولیه، کک است که از تقطیر آهسته زغالسنگ به دست میآید. در سالهای اخیر، کاهش منابع زغالسنگهای کک شو موجب افزایش قیمت کک شده است.
معادن استخراج آهن در ایران و جهان
ایران از نظر میزان ذخایر سنگ آهن، نهمین کشور دنیا بوده و ۲ درصد از کل این منابع را در خود جای داده و این ذخایر در نقاط زیادی از کشور شناسایی شده است.
معدن سنگ آهن چغارت بافق یزد، اولین معدن سنگ آهن ایران است که شرکت ذوب آهن اصفهان را در زمان تاسیس این شرکت تغذیه میکرد. این معدن با دارا بودن بیش از یک سوم ذخایر سنگ آهن در کل کشور، مهمترین معدن سنگ آهن در ایران به شمار میرود.
معدن سنگ آهن چادرملو که در کویر مرکزی واقع شده، در حال حاضر بزرگترین تولیدکننده کنسانتره سنگ آهن در کشور به شمار میرود. موجودی ذخایر قابل استخراج در این معدن ۳۲۰ تن است که پیشبینی میشود تا ۱۰ سال آینده به پایان برسد.
معدن سنگ آهن گل گهر که در شهرستان سیرجان قرار دارد، با ذخیره احتمالی ۱ میلیارد تن و ذخیره قطعی ۲۱۹ میلیون تن، برزگترین معدن شناخته شده سنگ آهن در خاورمیانه است. این معدن تولیداتی به صورت گندله، کنستانتره و سنگ دانهبندیشده دارد.
معدن سنگ آهن سنگان، در ۲۵۰ کیلومتری مشهد قرار داشته و ذخایر آهنی موجود در آن به دو تیپ تقسیم شده است؛ تیپ اول، میانگین عیار ۵۳ و تیپ دوم با عیار ۳۳ دارد. معادن سنگان ۶۰۰ سال پیش با عنوان معادن سنگآهن خواف معرفی و عملیات اکتشاف اولیه آن بین سالهای ۱۳۵۰ تا ۱۳۵۸ صورت گرفت. میزان ذخیره زمینشناسی این معدن ۲/۱ میلیارد تن برآورد شده است.
در حال حاضر، عملیات استخراج آهن در ۴۸ کشور دنیا، از جمله ایران صورت میگیرد که بیش از ۹۸ درصد آن در صنعت فولادسازی کاربرد دارد. روشهای استخراج، تولید آهن و فولاد در طی زمان و با پیشرفت تکنولوژی دستخوش تغییر شده و این تغییرات امروزه در جهت افزایش بازدهی تولید و همچنین کاهش مضرات زیستمحیطی این صنعت عظیم هستند. چالش مهمی که در این زمینه وجود دارد، کاهش ذخایر سنگ آهن موجود در جهان است. به نظر شما در صورت اتمام این منابع، قیمت ضایعات آهن و فلزات به چه سمتی تغییر میمند و آیا بازیافت آنها میتواند به طور کامل پاسخگوی نیاز روزافزون صنایع و بخشهای مختلف باشد؟