آهن از چه سنگی استخراج میشود
آهن، فلزی است که ارزش و نقش حیاتی آن در تمامی بخشهای اقتصادی و اجتماعی بر کسی پوشیده نیست. به طوری که خود کفایی و پویا بودن یک کشور در استخراج آهن، موفقیت و پویایی صنایع وابسته را در پی خواهد داشت. به دست آوردن سنگ معدنی این فلز از اعماق معادن و تبدیل آن به قطعات مستحکمی که به صورت آلیاژهای مختلف در اتومبیلسازی، ساختمانسازی، پلسازی، کشتیسازی و… قابل استفاده باشند، مستلزم طی کردن فرآیندهای فیزیکی، شیمیایی و مکانیکی ویژهای است. در این مقاله، عملیات و مراحل مختلف استخراج آهن، از معدن تا کارخانه را مورد بررسی قرار داده و به جزئیات مهم آنها میپردازیم.
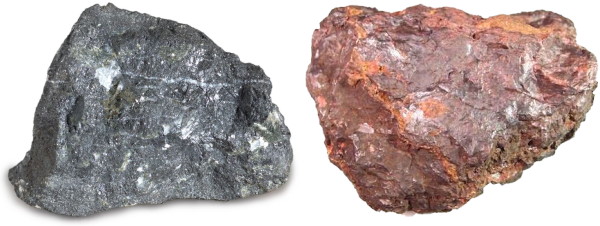
سنگ آهن چیست و انواع آن
سنگ آهن (Iron ore) یکی از فراوانترین سنگهای معدنی در زمین است که تشکیل آن به تدریج و در طی سالهای طولانی صورت میگیرد. و دیگر محصولات نهایی به دست آمده، به ارزش سنگ آهن وابسته است. حدود ۵ درصد از پوسته کره زمین را اکسیدهای آهن تشکیل میدهند. علاوه براکسید، آهن به شکلهای ترکیبی دیگری مانند سولفوریا سولفید، کربنات، سیلیکات وآرسنیکی نیز یافت میشود. به طور کلی تمام سنگهای پوسته به استثنای برخی سنگهای آهکی، حاوی مقداری آهن در ترکیب خود هستند. استخراج روباز (سطحی) و استخراج زیرزمینی دو روش اصلی برای استخراج سنگ آهن هستند که با توجه به عمق سنگ آهن، شکل آن و مسائل اقتصادی، میتوان آنها را به کار برد.
بالغ بر ۳۰۰ نوع کانی آهندار در طبیعت یافت میشود که نوع ترکیب و عیار (درصد آهن خالص موجود در سنگ آهن) آنها با یکدیگر متفاوت است و فقط تعداد معدودی از آنها که به طور کلی اکسیدهای آهن هستند، قابلیت تصفیه و جداسازی آهن موجود را دارند. از ترکیبات زیر میتوان به عنوان مهمترین کانیهای اکسیدی نام برد: مگنتیت و هماتیت نسبت با سایر کانیها از اهمیت بیشتری برخوردار مگنتیت به علت خاصیت احیاپذیری کم، به صورت مستقیم کاربرد ندارد و باید تحت عملیات کلوخهسازی یا گندلهسازی قرار بگیرد تا شکل کانیشناسی آن عوض شود. اولین قدم در جهت استخراج آهن، شناسایی معادن بالقوه آن و نوع کانیهای موجود در این معادن است. روشهای متعددی برای شناسایی این معادن وجود دارد، مانند:
- عکسبرداری هوایی
- برداشت زمینشناسی
- ژئوشیمی
- بیوژئوشیمی
- برداشت الکتریکی
- برداشت ژئوفیزیک
- حفر گمانه
معدن یا همان کانسار آهن میتواند نزدیک سطح (تا عمق ۱۰۰۰ متر) یا اعماق زمین (تا عمق ۲۰۰۰ متر) قرار داشته باشد. این عمق قرارگیری و همچنین شکل و عیار کانسار، در نحوهی استخراج آهن تاثیرگذار هستند. عیار ۷۰ درصد به عنوان یک عیار مطلوب و اقتصادی برای استخراج آهن در نظر گرفته میشود و در صورتی که مقدار عیار از ۶۰ درصد پایینتر باشد، استخراج سنگ آهن اقتصادی نخواهد بود.این سنگ که در واقع حاوی رگههای از آهن میباشد از معادن استخراج میشود و پس از فرآوری و خالصسازی، برای تولید انواع سازههای فلزی مورد استفاده قرار میگیرد. در این مقاله قصد داریم به بررسی چگونگی استخراج، فرآوری و کاربردهای آن پرداخته و توضیحاتی خدمت شما ارائه دهیم.
در این روش که به آن احیای غیرمستقیم نیز گفته میشود، آهن خام مذاب به دست آمده از فرآیند کوره بلند را درون کوره اکسیژنی میریزند و با دمش گاز اکسیژن خالص، کربن و ناخالصیهای اضافی آن را میسوزانند. در نتیجه کربن فولاد به مقدار موردنظر میرسد. سپس با افزودن عناصر آلیاژی، استحکام فولاد را افزایش میدهند. این تکنولوژی مهمترین شیوه تولید فولاد خام در جهان است که بیش از ۶۰ درصد از کل فولاد خام دنیا با استفاده از آن تولید میشود. تولید فولاد با این فرآیند، از نظر نرخ تولید بازدهی بالایی دارد؛ اما نیازمند مواد خام باکیفیت است. یکی از این مواد اولیه، کک است که از تقطیر آهسته زغالسنگ به دست میآید. در سالهای اخیر، کاهش منابع زغالسنگهای کک شو موجب افزایش قیمت کک شده است.
در حال حاضر، عملیات استخراج آهن در ۴۸ کشور دنیا، از جمله ایران صورت میگیرد که بیش از ۹۸ درصد آن در صنعت فولادسازی کاربرد دارد. روشهای استخراج، تولید آهن و فولاد در طی زمان و با پیشرفت تکنولوژی دستخوش تغییر شده و این تغییرات امروزه در جهت افزایش بازدهی تولید و همچنین کاهش مضرات زیستمحیطی این صنعت عظیم هستند. چالش مهمی که در این زمینه وجود دارد، کاهش ذخایر سنگ آهن موجود در جهان است. به نظر شما در صورت اتمام این منابع، و فلزات به چه سمتی تغییر میمند و آیا بازیافت آنها میتواند به طور کامل پاسخگوی سنگ آهن یا Iron Ore یکی از مواد معدنی محبوب و پرکاربرد و از فراوان ترین سنگهای موجود روی زمین میباشد که حدود 5 درصد از پوسته زمین را تشکیل میدهد.
سنگ آهن چیست؟
سنگ آهن به عنوان ماده اولیه تولید فولاد شناخته میشود و حدود 98 درصد از استخراج این ماده در جهان به منظور تولید فولاد انجام میشود. فلز فولاد تولید شده نیز کاملا قابل بازیافت میباشد و میتوان از آن به عنوان مواد اولیه تولید محصولات فولادی با همان کیفیت اولیه استفاده کرد. این عنصر به راحتی اکسید میشود و از آلیاژ آن که با استفاده از عنصرهای مختلف به خصوص نیکل و کروم تهیه میشود جهت افزایش استحکام ساختمان و موارد دیگر استفاده میشود. این سنگ معدنی در حدود 50 کشور جهان استخراج میشود و کشورهای استرالیا و برزیل به عنوان بزرگترین صادرکنندههای این محصول و کشور چین به عنوان بزرگترین واردکننده آن شناخته میشوند.
کاربرد سنگ آهن
همانطور که اشاره کردیم کاربرد اصلی سنگ آهن در تولید فلز آهن و میباشد. از فولاد نیز در ساخت ماشین آلات، ، ، مانند راهآهن، لوکوموتیو و کشتی، مبلمان و غیره استفاده میشود. به جز موارد فوق از آهن پودر شده در ساخت انواع خاصی از فولادها، مگنتها، کاتالیستها، از آهن رادیواکتیو در داروسازی تحت عنوان یک عنصر ردیاب در تحقیقات بیوشیمی و فلزکاری، از اکسید آهن سیاه در فلزکاری، استفاده به عنوان رنگدانه در ترکیبات پولیش، ساخت جوهرهای مغناطیسی در صنعت الکترونیک و از آهن قرمز برای استفاده در جوهر پرینت، لوازم آرایشی و رنگهای نقاشی استفاده میشود.
استخراج آهن از سنگ آهن
برای استفاده از سنگ آهن، خالصسازی آن ضروری میباشد. استخراج آهن از سنگ معدن آهنی( به سنگهایی که بیشتر از 20 درصد آهن داشته باشند سنگ معدن آهنی گفته میشود) به وسیله فرایندهای فیزیکی، مکانیکی و شیمیایی ویژه انجام میشود که در فرایند شیمیایی، سنگ های اکسیدی آهن توسط کربن احیا و عنصر آهن آزاد می شود. قرنها از زغال چوب برای احیا استفاده میشد ولی از اوایل قرن نوزدهم کک جایگزین زغال چوب میشود و مورد استفاده قرار میگیرد. برای تولید و خالص کردن سنگآهن باید فرایند ذوب و احیا در کورهها انجام گیرد. روشهای مختلفی برای انجام این فرایند موجود است ولی کوره بلند به عنوان اصلی ترین روشهای جداسازی آهن از سنگ معدنی آن به کار برده میشود.
فرآوری سنگ آهن
با توجه به پایین بودن عیار سنگ آهن، خالص نبودن آنها، داشتن ترکیبات مضر و همچنین راحت تر کردن استفاده از آن در مکانهای مختلف، عملیات فرآوری انجام داده میشود. پس از فرآوری، سنگ آهن از لحاظ ظاهری به صورت شکلهای مختلفی از جمله دانهبندی شده، گندله، کلوخه و کنسانتره تولید می گردد و مصرف کنندگان با توجه به نیاز خود این محصول را تهیه کرده و از آن استفاده میکنند. در ادامه به بررسی این اشکال میپردازیم. سنگ آهن دانهبندی شده برای تولید سنگ آهن دانهبندی شده از روش بدون آب و خشک استفاده میشود. این نوع کانی به دلیل داشتن عیار پایین در سیستم احیا قابل استفاده نمیباشد و به دلیل خاصیت احیا پذیری پایین کمتر مورد استفاده قرار میگیرد.
کنسانتره برای تولید کنسانتره از آب استفاده میشود و مراحل فرآوری آن شامل خرد کردن، آسیاب کردن، پرعیارسازی، آبگیری میباشد. کنسانتره به دلیل داشتن عیار مناسب در مصارف مختلفی قابل بهره برداری میباشد. کلوخه کلوخه رایج ترین روش استفاده از سنگ آهن میباشد و سالانه صدها میلیون تن از آن تولید میشود و مورد استفاده قرار میگیرد. گندله گندله از نرمه و سایر مواد افزودنی تولید میشود، به شکل گلوله بوده که در ابتدا خام میباشد، سپس پخته و سخت میشود و جهت احیا، به روش سنتی تولید آهن در کوره بلند یا روش احیای مستقیم به کار می رود.
انواع سنگ آهن
سنگ آهنها دارای انواع مختلفی میباشند و در دو دسته قابل طبقهبندی میباشند.
- از لحاظ شکل ظاهری: شامل دانهبندی شده، گندله، کلوخه و کنسانتره که درباره آنها توضیح داده شد.
- از لحاظ نوع کانی: شامل هماتیت، مگنتیت، زئولیت، لیمونیت، سیدریت.
هماتیت و مگنتیت در حال حاضر به عنوان با ارزشترین سنگ آهنهای موجود شناخته میشوند و درصد آهن آنها حدود 70 درصد میباشد. در ادامه به بررسی این دو سنگ خواهیم پرداخت. هماتیت هماتیت یکی از کانیهای سنگ آهن میباشد. هماتیت به وسیله اسید کلریک و آب تمیز شده و به عنوان رنگدانه نیز استفاده میشود. دانه دانه بودن و فلس داشتن از ویژگیهای ظاهری این محصول میباشد و قابلیت تغییر رنگ از نقره استیل تا قهوهای مایل به قرمز را دارد. غیرمغناطیسی و ضدزنگ بودن از ویژگیهای هماتیت میباشد.
جمع بندی
در این مقاله تلاش بر این شد که شما را با سنگ معدنی ، کاربردهای آن و همچنین نحوه فرآوری و انواع آن آشنا کنیم و اطلاعات مختصر و مفیدی را درباره این نوع سنگ در اختیار شما قرار دهیم. در صورت نیاز به دریافت مشاوره درباره انواع مقاطع فولادی و اطلاع از قیمت آهن آلات امروز و محصولات موجود به سایت مراجعه کنید. نیاز روزافزون صنایع و بخشهای مختلف باشد؟ مگنتیت مگنتیت به رنگ سیاه بوده و مغناطیسی بودن خاصیت ویژه آن به شمار میآید. از مگنتیت به خاطر ویژگی مغناطیسی بودن در موارد مختلف به خصوص تولید آهنربا استفاده میشود. در کشور ایران ذخایر مگنتیت بیشتر بوده و به دلیل فرآوری راحتتر نسبت به هماتیت، تمایل بازار داخلی به این نوع سنگ آهن بیشتر میباشد.