چک لیست تعمیر و نگهداری ماشین آلات تزریق پلاستیک
چک لیست تعمیر و نگهداری ماشین آلات تزریق پلاستیک
تزریق پلاستیک سودآور است ، زیرا این فرآیند به تولید انبوه قطعات پلاستیکی با هزینه کم و دقت بالا کمک میکند.همچنین این دستگاه با بهره وری بالا و استراتژی ارزیابی موثر میتواند درآمد ماهیانه دستگاه تزریق پلاستیک به چند صد میلیون تومان برساند.
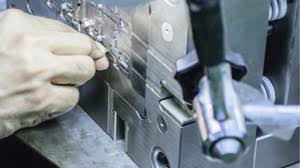
نظافت و تمیزکاری
یکی از مهم ترین مراحل در تعمیر و نگهداری دستگاه های تزریق پلاستیک، نظافت و تمیزکاری منظم آن ها است. در ادامه به نکات کلیدی در زمینه نظافت و تمیزکاری این دستگاه ها پرداخته می شود:
تمیز کردن دستگاه پس از هر شیفت کاری:
پس از پایان هر شیفت کاری، تمیز کردن دستگاه های تزریق پلاستیک برای جلوگیری از تجمع مواد پلاستیکی، گرد و غبار، و سایر ذرات ضروری است. این مواد می توانند به مرور زمان در دستگاه انباشته شده و عملکرد آن را مختل کنند. بهتر است که اپراتورها به طور منظم و دقیق پس از هر شیفت، دستگاه را تمیز کنند تا از خرابی های ناگهانی جلوگیری شود.
تمیز کردن قالب ها:
قالب ها که بخش اصلی تولید محصول هستند، باید به طور مداوم از هرگونه آلودگی و مواد اضافی پاک شوند. مواد پلاستیکی ذوب شده ممکن است به سطح قالب بچسبند و باعث ایجاد نقص در تولید قطعات شوند. استفاده از محلول های پاک کننده مناسب و همچنین برس های مخصوص برای پاک کردن این مواد از اهمیت زیادی برخوردار است. تمیز نگه داشتن قالب ها نه تنها کیفیت محصولات تولیدی را افزایش می دهد، بلکه عمر قالب ها را نیز بهبود می بخشد.
بررسی نشت:
در فرآیند تزریق پلاستیک، نشت مواد از سیستم های مختلف دستگاه می تواند مشکلات جدی ایجاد کند. به ویژه، بررسی نشت مواد پلاستیکی و روغن از سیستم های مختلف دستگاه باید به طور منظم انجام شود. نشت مواد می تواند باعث توقف غیرمنتظره دستگاه یا حتی خرابی های شدیدتر شود. در صورت مشاهده نشت، باید بلافاصله اقدام به تعمیر و تعویض قطعات آسیب دیده کرد.
تست روغن:
روغن ها در دستگاه های تزریق پلاستیک برای روان کاری قطعات متحرک استفاده می شوند. تمیز نگه داشتن و بررسی منظم سطح روغن و کیفیت آن از اهمیت بالایی برخوردار است. در صورت کثیف شدن یا پایین آمدن سطح روغن، عملکرد دستگاه مختل می شود. تعویض منظم روغن بر اساس برنامه های نگهداری توصیه شده، به بهبود عملکرد دستگاه و کاهش خرابی ها کمک می کند.
بررسی سیستم های هیدرولیک
سیستم های هیدرولیک نقش بسیار حیاتی در عملکرد دستگاه های تزریق پلاستیک دارند. این سیستم ها وظیفه دارند تا نیروی لازم برای حرکت قسمت های مختلف دستگاه را تامین کنند. بررسی و نگهداری منظم سیستم های هیدرولیک نه تنها به افزایش عمر مفید دستگاه کمک می کند، بلکه از بروز خرابی های ناگهانی و توقف عملیات جلوگیری می کند.
بررسی نشت: اطمینان از عدم وجود نشت در سیستم هیدرولیک
نشت روغن هیدرولیک می تواند نشانه ای از خرابی یا فرسایش قطعاتی مانند شیلنگ ها، پمپ ها و اتصالات باشد. نشت مایعات هیدرولیک باعث کاهش فشار در سیستم و کاهش کارایی دستگاه می شود و می تواند منجر به خرابی های جدی شود. به همین دلیل، در صورت مشاهده نشت، باید به سرعت اقدامات لازم برای تعمیر و تعویض قطعات انجام شود.
تست روغن: انجام آزمایش های منظم روی روغن هیدرولیک
روغن هیدرولیک نه تنها برای روان کاری قطعات، بلکه برای انتقال نیرو نیز استفاده می شود. تست منظم روغن برای اطمینان از اینکه آلودگی یا تغییرات غیرمطلوب در آن وجود ندارد، از اهمیت بالایی برخوردار است. در صورت مشاهده هرگونه آلودگی، تغییر رنگ یا کاهش سطح روغن، باید بلافاصله روغن تعویض شود. تعویض به موقع روغن هیدرولیک از خرابی قطعات جلوگیری کرده و عملکرد دستگاه را بهبود می بخشد.
تنظیم فشار سیستم هیدرولیک:
فشار نامناسب می تواند به قطعات داخلی سیستم فشار وارد کرده و باعث خرابی سریع تر آن ها شود. در دستگاه های تزریق پلاستیک، عدم تنظیم صحیح فشار هیدرولیک می تواند به مشکلات جدی در فرآیند تزریق و کیفیت محصول نهایی منجر شود. استفاده از مانومترهای دقیق و تجهیزات استاندارد برای تنظیم و نظارت بر فشار سیستم ضروری است.
بررسی سلامت شیلنگ ها و اتصالات:
شیلنگ ها و اتصالات در سیستم هیدرولیک ممکن است به مرور زمان دچار ساییدگی و فرسایش شوند. بررسی منظم وضعیت شیلنگ ها برای شناسایی هرگونه ترک خوردگی، خم شدگی یا آسیب بسیار مهم است. در صورت مشاهده هرگونه خرابی، باید شیلنگ ها و اتصالات بلافاصله تعویض شوند تا از بروز حوادث ناگوار و خرابی های بیشتر جلوگیری شود.
در نتیجه، سیستم هیدرولیک یکی از اجزای اصلی و حیاتی دستگاه تزریق پلاستیک است که نیاز به نگهداری و بررسی دقیق دارد.
بررسی سیستم های الکتریکی
سیستم های الکتریکی دستگاه های تزریق پلاستیک بخش دیگری از اجزای حیاتی این دستگاه ها هستند که عملکرد صحیح آن ها برای بهره وری دستگاه و ایمنی اپراتورها بسیار مهم است. سیستم های الکتریکی مسئول کنترل عملکردهای مختلف دستگاه، تأمین انرژی و ایجاد هماهنگی بین بخش های مختلف دستگاه هستند. در این بخش به مهم ترین نکات مربوط به بررسی و نگهداری سیستم های الکتریکی پرداخته می شود:
بررسی اتصالات: اطمینان از سالم بودن اتصالات الکتریکی
اتصالات الکتریکی دستگاه تزریق پلاستیک باید به طور منظم بررسی شوند تا از سالم بودن آن ها اطمینان حاصل شود. اتصالات الکتریکی ضعیف یا فرسوده می تواند منجر به قطع و وصل های ناگهانی برق، ایجاد جرقه، یا حتی آتش سوزی شود. سیم کشی ها و اتصالات باید به طور مرتب از نظر سایش، خوردگی یا خرابی بررسی شوند.
تست عملکرد: بررسی صحت عملکرد سیستم های الکتریکی
عملکرد صحیح سیستم های الکتریکی باید به طور منظم آزمایش شود. این شامل تست کلیه سنسورها، کنترلرها، پنل های کنترلی و مدارهای الکتریکی دستگاه است. هر گونه نقص در عملکرد این بخش ها می تواند منجر به توقف تولید، مشکلات کیفیتی در محصولات و حتی بروز خطرات ایمنی برای کارکنان شود.
بررسی فیوزها و کلیدهای حفاظتی:
فیوزها و کلیدهای حفاظتی به عنوان اولین خط دفاعی در برابر افزایش جریان الکتریکی و جلوگیری از آسیب به دستگاه عمل می کنند. این اجزا باید به طور مرتب بررسی شوند تا از سالم بودن آن ها اطمینان حاصل شود. در صورت سوختن فیوزها یا خرابی کلیدهای حفاظتی، آن ها باید بلافاصله تعویض شوند تا از بروز حوادث ناشی از نوسانات برق و افزایش جریان جلوگیری شود.
نگهداری و تمیزکاری تابلوهای برق:
تابلوهای برق دستگاه های تزریق پلاستیک به مرور زمان ممکن است دچار تجمع گرد و غبار شوند که این موضوع می تواند به مشکلات جدی الکتریکی منجر شود. نگهداری و تمیزکاری منظم تابلوهای برق و استفاده از محفظه های مناسب برای محافظت از تجهیزات الکتریکی در برابر گرد و غبار و رطوبت از اهمیت بالایی برخوردار است.
بازرسی دوره ای کابل ها و سیم ها:
کابل ها و سیم ها نیز باید به طور دوره ای از نظر سلامت بررسی شوند. هر گونه پارگی، ساییدگی یا خرابی در سیم ها می تواند منجر به اتصال کوتاه یا نوسانات الکتریکی خطرناک شود. بررسی منظم و تعویض کابل ها و سیم های آسیب دیده از خرابی های جدی جلوگیری کرده و ایمنی سیستم را حفظ می کند.
بازرسی سیستم های قالب
سیستم های قالب یکی از بخش های حیاتی در دستگاه های تزریق پلاستیک هستند، چرا که کیفیت محصول نهایی به کارکرد صحیح و دقیق قالب ها بستگی دارد. نگهداری و بازرسی منظم این سیستم ها باعث می شود که هم کارایی دستگاه بهبود یابد و هم عمر مفید قالب ها افزایش پیدا کند. در این بخش به مهم ترین نکات مربوط به بازرسی سیستم های قالب پرداخته می شود:
بازرسی سایش: بررسی اجزای قالب برای شناسایی سایش یا آسیب
یکی از مشکلات رایج در سیستم های قالب، سایش قطعات است. این مشکل به مرور زمان به دلیل فشار و تماس مکرر بین قطعات متحرک قالب و مواد مذاب پلاستیکی رخ می دهد. سایش بیش از حد می تواند به خرابی قالب و افت کیفیت قطعات تولیدی منجر شود. بررسی منظم و دقیق اجزای قالب از نظر سایش و آسیب های احتمالی می تواند از بروز این مشکلات جلوگیری کند. در صورت مشاهده هرگونه سایش، قطعات آسیب دیده باید تعمیر یا تعویض شوند.
تعویض قطعات فرسوده: تعویض قطعاتی که شناسایی شده اند نیاز به تعمیر دارند
قطعاتی که دچار سایش یا خرابی شده اند باید به سرعت تعویض شوند تا از تاثیر منفی آن ها بر عملکرد دستگاه و کیفیت محصول جلوگیری شود. این قطعات ممکن است شامل صفحات قالب، پین های هدایت کننده یا قطعات دیگر باشند. عدم تعویض به موقع قطعات فرسوده می تواند باعث ایجاد توقف های غیرمنتظره در فرآیند تولید و افزایش هزینه های نگهداری شود.
تمیزکاری قالب ها:
یکی از عوامل کلیدی در عملکرد صحیح قالب ها، تمیزکاری منظم آن هاست. مواد پلاستیکی مذاب ممکن است در طول زمان به قالب بچسبند و باعث کاهش کیفیت تولید شوند. پاک سازی دقیق قالب ها بعد از هر دوره تولید باعث حفظ دقت و کیفیت تولید و جلوگیری از خرابی های طولانی مدت می شود.
بازرسی سطوح قالب:
بررسی سطوح داخلی و خارجی قالب ها برای شناسایی هرگونه خوردگی یا ترک بسیار مهم است. سطوح آسیب دیده می توانند باعث کاهش دقت در تولید و افت کیفیت قطعات تولیدی شوند. هرگونه ترک خوردگی یا خوردگی باید بلافاصله شناسایی و تعمیر شود تا از خرابی های جدی تر جلوگیری گردد.
بررسی تراز قالب ها:
تراز بودن دقیق قالب ها برای تولید قطعات با کیفیت بسیار حیاتی است. عدم تراز صحیح قالب ها می تواند باعث ایجاد نقص در قطعات نهایی شود و تولید را مختل کند. بنابراین، بررسی و تنظیم تراز قالب ها باید به طور منظم انجام شود تا از بروز مشکلات جلوگیری شود.
روان کاری اجزای متحرک قالب:
قطعات متحرک قالب نیاز به روان کاری مناسب دارند تا به صورت نرم و بدون ایجاد سایش یا خرابی کار کنند. استفاده از روان سازهای مناسب و با کیفیت و همچنین بررسی منظم وضعیت روان کاری اجزا می تواند از بروز سایش و فرسایش در این قطعات جلوگیری کند.
بررسی سیستم خنک کننده
سیستم خنک کننده در دستگاه های تزریق پلاستیک نقش بسیار مهمی در کنترل دمای فرآیند و بهبود کیفیت محصول نهایی دارد. عملکرد صحیح این سیستم باعث می شود که قالب ها و مواد پلاستیکی به طور یکنواخت خنک شوند و محصول نهایی بدون نقص تولید شود. همچنین، نگهداری منظم سیستم خنک کننده می تواند از خرابی های ناشی از گرمای بیش از حد جلوگیری کند. در این بخش به نکات کلیدی برای بازرسی و نگهداری سیستم خنک کننده پرداخته می شود:
بررسی کانال های خنک کننده: چک کردن کانال های خنک کننده برای جلوگیری از گرفتگی ها
کانال های خنک کننده که معمولاً در قالب ها قرار دارند، مسئول انتقال آب یا سایر مایعات خنک کننده برای کنترل دمای فرآیند هستند. با گذشت زمان، ممکن است این کانال ها به دلیل تجمع رسوبات، آلودگی یا ذرات خارجی مسدود شوند که باعث کاهش کارایی خنک کننده می شود. بازرسی منظم کانال ها و استفاده از محلول های تمیزکننده مناسب برای رفع گرفتگی ها، عملکرد سیستم خنک کننده را بهینه نگه می دارد.
شستشوی سیستم: شستشوی منظم سیستم خنک کننده برای حفظ کنترل دما
یکی از بهترین راه ها برای حفظ عملکرد سیستم خنک کننده، شستشوی منظم آن است. این شستشوها به حذف رسوبات، آلودگی ها و ذرات خارجی که ممکن است در کانال های خنک کننده تجمع پیدا کنند، کمک می کند. استفاده از مواد تمیزکننده مناسب و آب با کیفیت بالا در فرآیند شستشو می تواند طول عمر سیستم خنک کننده را افزایش داده و از بروز خرابی های زودرس جلوگیری کند.
بررسی کیفیت و دمای مایع خنک کننده:
مایعات خنک کننده مورد استفاده در سیستم باید از کیفیت بالایی برخوردار باشند. استفاده از آب با املاح زیاد یا مایعات خنک کننده غیراستاندارد می تواند منجر به ایجاد رسوبات و کاهش کارایی سیستم خنک کننده شود. علاوه بر این، دمای مایع خنک کننده باید به طور منظم کنترل شود تا از خنک سازی یکنواخت و موثر اطمینان حاصل شود.
بازرسی پمپ ها و لوله های سیستم خنک کننده:
پمپ های سیستم خنک کننده مسئول جریان دهی مایعات خنک کننده در سراسر دستگاه هستند. عملکرد نامناسب پمپ ها یا وجود نشتی در لوله های خنک کننده می تواند منجر به کاهش عملکرد سیستم شود. بنابراین، بازرسی منظم پمپ ها و لوله ها برای شناسایی هرگونه نشتی، خرابی یا کاهش فشار بسیار حیاتی است. در صورت مشاهده مشکلات، تعویض یا تعمیر به موقع ضروری است.
کنترل و تنظیم جریان مایع خنک کننده:
میزان جریان مایع خنک کننده باید به دقت تنظیم شود تا اطمینان حاصل شود که دما به طور یکنواخت در کل فرآیند کنترل می شود. جریان بیش از حد یا کمتر از حد نیاز می تواند منجر به خنک سازی نابرابر و ایجاد نقص در محصول نهایی شود. استفاده از تجهیزات مانیتورینگ جریان و دما برای کنترل دقیق عملکرد سیستم خنک کننده ضروری است.
ثبت سوابق نگهداری
یکی از مهم ترین مراحل در نگهداری و تعمیرات دستگاه های تزریق پلاستیک، ثبت سوابق نگهداری است. این مرحله به تیم های فنی و مدیریتی کمک می کند تا تمامی فعالیت های نگهداری و تعمیراتی که روی دستگاه ها انجام شده است را ثبت و مستندسازی کنند. ثبت دقیق و منظم این سوابق باعث می شود که تعمیرات به موقع انجام شده و از بروز خرابی های ناگهانی جلوگیری شود. در این بخش به اهمیت و چگونگی ثبت سوابق نگهداری می پردازیم:
نگهداری سوابق: ثبت فعالیت های نگهداری و تعمیرات انجام شده
هرگونه فعالیت نگهداری یا تعمیراتی که روی دستگاه های تزریق پلاستیک انجام می شود، باید به طور دقیق در سوابق نگهداری ثبت شود. این سوابق شامل تاریخ انجام فعالیت، نوع تعمیر یا نگهداری، قطعات تعویض شده، نام تکنسین مسئول و نتایج بررسی ها است. داشتن چنین سوابقی به تیم فنی کمک می کند تا اطلاعات کاملی درباره وضعیت دستگاه داشته باشند و برنامه های تعمیرات بعدی را بهتر برنامه ریزی کنند.
شناسایی مشکلات: شناسایی مشکلات مکرر از طریق سوابق نگهداری
یکی از مزایای مهم ثبت سوابق نگهداری، شناسایی مشکلات مکرر یا خرابی های مشابه در دستگاه ها است. اگر یک قطعه یا بخش خاصی از دستگاه به طور مکرر دچار مشکل شود، می توان از طریق بررسی سوابق نگهداری این مشکل را شناسایی کرده و راه حل های پیشگیرانه یا بهبود یافته ای برای جلوگیری از تکرار آن در نظر گرفت. این کار به کاهش هزینه های تعمیرات و افزایش بهره وری دستگاه کمک می کند.
مطلبتون خیلی خوب بود. من به عنوان یک متخصص مدیریت دارایی، می دونم که مدیریت دارایی های فیزیکی خیلی مهمه. آیا شما می تونید در مورد ارتباط بین چک لیست تعمیر و نگهداری و مدیریت دارایی های فیزیکی بیشتر توضیح بدید؟
سلام. مطلبتون خیلی خوب بود. من به عنوان یک کارشناس استانداردها، به این موضوع علاقه مندم که بدونم آیا استانداردهای خاصی برای تعمیر و نگهداری دستگاه های تزریق پلاستیک وجود داره یا نه؟
آیا شما می تونید در مورد استفاده از سنسورها و سیستم های مانیتورینگ برای پیش بینی خرابی ها بیشتر توضیح بدید؟
من به عنوان یک مهندس تعمیرات، بهتون پیشنهاد می کنم که در مورد تحلیل روغن استفاده شده در دستگاه بیشتر توضیح بدید. تحلیل روغن می تونه اطلاعات مفیدی در مورد وضعیت داخلی دستگاه به ما بده.
من به عنوان یک مهندس مکانیک، می دونم که ارتعاشات می تونه به دستگاه آسیب برسونه. آیا شما می تونید در مورد بررسی ارتعاشات دستگاه بیشتر توضیح بدید؟
به نظر من، یکی از مهم ترین بخش های چک لیست، بررسی روغن کاری قطعات متحرکه هست. روغن کاری به موقع باعث میشه که دستگاه روان تر کار کنه و عمر قطعات افزایش پیدا کنه.
من تازه وارد این حوزه شدم و این مطلب برام خیلی مفید بود. حالا می دونم که باید به چه نکاتی موقع کار با دستگاه تزریق پلاستیک توجه کنم.
خیلی ممنون از این مطلب جامع و کاربردی. من یه سوال داشتم که آیا این چک لیست برای همه نوع دستگاه تزریق پلاستیک یکیه یا متفاوت هست؟
این مطلب خیلی به درد کارگاه های تولیدی می خوره. با رعایت این نکات می تونن هزینه های تعمیر و نگهداری رو کاهش بدن و تولیدشون رو افزایش بدن.
مطلب خیلی خوبی بود. حالا متوجه شدم که چک لیست تعمیر و نگهداری چقدر مهمه. با استفاده از این چک لیست میتونیم از خرابی های ناگهانی دستگاه جلوگیری کنیم و طول عمر دستگاه رو افزایش بدیم.