نحوه ساخت کفش ایمنی
شرایط واردات کفش ایمنی
طبق قانون صادرات و واردات وزارت بازرگانی محدودیت خاصی جهت واردات محصول مورد مطالعه این طرح وجود ندارد و لذا امکان واردات و خرید کفش ایمنی خارجی با پرداخت حقوق گمرکی وجود دارد.
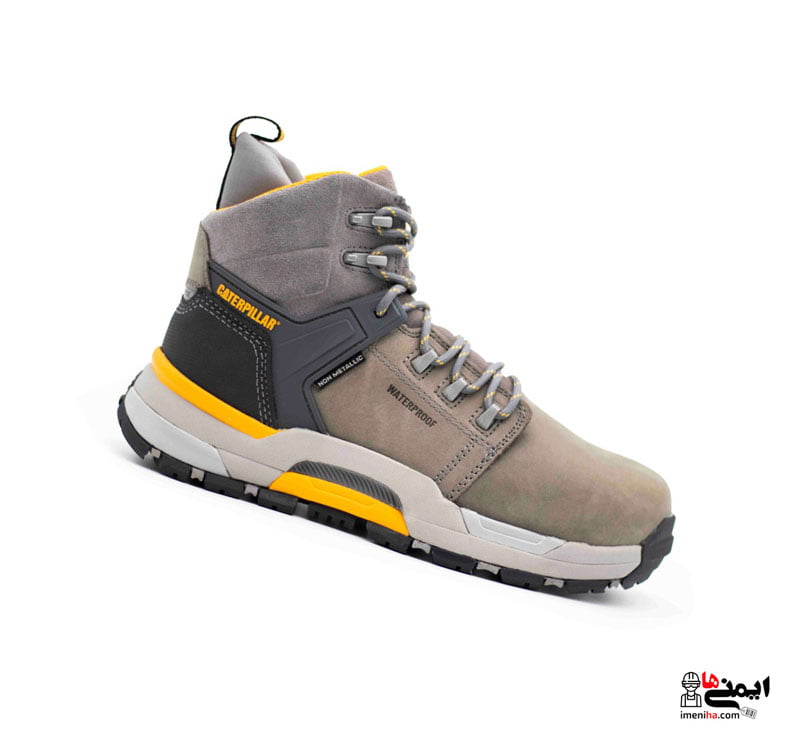
معرفی موارد مصرف و کاربرد کفش ایمنی
بر اساس دسته بندی انجام شده توسط اداره خدمات فنی بخش ایمنی وزارت کار ایالات متحده آمریکا، کفش های ایمنی بشرح ذیل تقسیم بندی می شود.
- کفش کارگری و کفش های ایمنی معمولی: این کفش ها ویژه شرایطی هستند که خطرات عمومی سقوط اجسام روی پاها وجود دارد البته در هنگام کار با اجسام بسیار سنگین مانند فلانج ها و قطعات فلزی بزرگ باید روی این کفش ها از یک روکش فلزی به نام متاتارسال استفاده شود.
- کفش های ایمنی ضد جرقه: : این کفش ها ویژه شرایطی می باشند که احتمال انفجار وجود دارد مانند محل های خطرناکی که کف آن عایق برق بوده و دارای سیستم اتصال به زمین (ارت) می باشند مانند کارگاه های ساخت ترکیبات قابل انفجار و هنگام تمیزکاری و پاکسازی تانک ها و مخازن بنزین و سایر هیدروکربن های فرار. تخت این کفش ها عایق بوده از قطعات فلزی مانند میخ و یراق در آنها استفاده نشده و پنجه آهنی آنها با یک فلز غیر آهنی پوشانده شده است.
- کفش های ایمنی برق: این کفش ها وظیفه به حداقل رساندن خطرات حاصل از تماس با جریان برق را دارند. در ساختمان این کفش ها از هیچ فلزی استفاده نشده است بجز در قسمت پنجه که از باقیمانده کفش عایق شده می باشد. این نوع کفش ها اگر در شرایط آب و هوایی مناسب بدرستی استفاده نگردد، ارزش حفاظتی خود را از دست می دهند.
- کفش های ایمنی ریخته گری و ذوب: این نوع کفش ها موسوم به گتردار و یا کنگره هستن و در محل های کاری مورد استفاده قرار می گیرند که کارگران با فلزات مذاب کار می کنند این کفش ها نباید دارای قید و بندها و محکم کننده های دست و پاگیر باشند و طرح ساختمان آنها باید به نحوی باشد که بتوان در شرایط اضطراری به سرعت آنها را از پا درآورد زیرا یکی از دلایل افزایش عارضه های جسمانی در هنگام ریختن مذاب روی کفش عدم امکان خارج نمودن سریع آن گزارش شده است.
- کفش های ایمنی رسانا: این نوع کفش ها با بدنه فلز جهت تخلیه شارژهای استاتیک (الکتریسیته ساکن) و برای کاستن از احتمال ایجاد جرقه های اصطحکاکی در محل های کاری که احتمال انفجار یا آتش سوزی وجود دارد مورد استفاده قرار می گیرند این کفش ها باید مورد آزمایش ادواری قرار گیرند تا اطمینان حاصل شود که مقاومت مجاز آنها از ٤٥٠ هزار اهم بیشتر نگردد.
- کفش های ایمنی ضد مواد شیمیایی: این نوع کفش ها ویژه مکان هایی می باشند که در آنجا با مواد شیمیایی بویژه اسیدها و قلیاها کار می شود جنس این کفش ها از لاستیک مصنوعی یا سایر مواد ترکیبی می باشد.
- کفش های ایمنی ویژه مانند کفش های با زیره تخت جهت کار بر روی سطوح داغ مانند آسفالت و کفش هایی با زیره های تقویت شده در مکان هایی که احتمال رفتن میخ و قطعات نوک تیز در پاها وجود دارد مورد استفاده قرار می گیرد.
کشورهای عمده تولید کننده و مصرف کننده کفش ایمنی
محصول تولیدی طرح کفش ایمنی می باشد که زیر مجموعه انواع کفش را شامل می گردد. کشورهای عمده تولیدکننده کفش ایمنی در جهان ایتالیا، اسپانیا، چین و ویتنام و واردکنندگان و مصرف کنندگان اصلی آن روسیه، آلمان،یونان، هلند و اسرائیل می باشند.
بررسی اجمالی تکنولوژی و روش تولید کفش کار
- بررسی سطح تکنولوژی تولید در واحدهای فعال
در تولید کفش های ایمنی هشت مرحله وجود دارد و کفش ها در خط تولید از مراحل مختلفی (که هریک در اتاق جداگانه ای انجام می گیرد) می گذرند، این مراحل شامل:
- برش این مرحله شامل برش ابتدایی چرم جهت حذف یکنواختی های موجود و برش ثانویه کلیه قطعات چرمی که توسط دستگاه مخصوص برش چرم و با استفاده از شابلون های مخصوص انجام می گیرد. ضخامت چرم رویه بسیار حائز اهمیت می باشد لذا جهت یکنواخت سازی ضخامت چرم که در نقاط مختلف متفاوت می باشد از دستگاه اشبالت استفاده می شود.
- جورکردن و دوختن پس از مرحله برش قطعات چرمی، لویس کاری، دوخت، منگنه و تکمیل رویه انجام می گیرد. در لویس کاری نقاطی که باید عملیات دوخت بر روی آن انجام گیرد نازک تر می شود که این عمل توسط ماشین لویس انجام گرفته و عمل دوخت توسط ماشین دوخت انجام گیرد. به منظور افزایش خاصیت انعطاف پذیری و قابلیت شکل پذیری چرم در حین عملیات کارکشی قراردادن چرم در محیطی که در آن بخار آب وجود داشته باشد ضروری می باشد. عملیات کارکشی بایستی پس از مدت کوتاهی از عملیات مرطوب نمودن انجام پذیرد تا از خروج رطوبت جلوگیری به عمل آید.
- جور کردن کفی در این مرحله کفی به کف قالب ماهیچه اتصال داده شده و عملیات چسب زنی لبه های تحتانی رویه و کفی عملیاتی می باشد که قبل از کارکشی انجام می گیرد.
- کارکشی بر روی قالب اصطلاح کارکشی به فرآیندی اطلاق می گردد که طی آن رویه چرمی با اعمال نیرو و ایجاد تنش های کششی در چرم بر روی قالب ماهیچه پلاستیک کشیده شده و در نتیجه لبه های اضافی تحتانی رویه به کفی کفش که به قالب ماهیچه متصل می باشد با استفاده از چسب و میخ متصل می گردد.
- در نتیجه انجام این عملیات رویه به محیط اطراف قالب کاملا فشرده شده و پس از درآوردن آن از قالب ماهیچه، شکل و فرم ظاهری ماهیچه را به خود گرفته و در مقابل تغییر شکل مقاومت می کند پس از این مرحله لازم است کیفیت کار انجام شده توسط مسئول کنترل کیفی انجام پذیرد و بعد از بازرسی های به عمل آمده قسمت جلوی پنجه کفش با گیره مخصوص توسط متصدی به زیر قالب انجام پذیرد.
- مرحله پنجه کشی توسط دستگاه پنجه کشی بعد از چسب زنی و آماده سازی لازم انجام می شود. کفش های ایمنی مقاوم در برابر ضربه دارای سرپنجه های فلزی می باشند که عملیات ساخت آن توسط واحدهای خارج از کارگاه تولیدی انجام می شود.
- تزریق زیره در این مرحله رویه و کفی متصل شده به یکدیگر در یک قالب زیره که طرح مورد نظر را داراست قرار می گیرد و مواد زیره توسط دستگاه تزریق در داخل آن تزریق شده و زیره بدین روش شکل می گیرد.
- تکمیل نهایی و بسته بندی در این مرحله اقدامات تکمیلی فرایند مانند پاشنه گذاری و بسته بندی کفش انجام می گیرد.
آزمون های کفش ایمنی
-
- آزمون فشردگی : در این آزمایش با استفاده از دستگاه آزمون فشردگی پنجه فولادی باید بین دو سطح موازی و افقی (فک) دستگاه قرار گرفته و فشار استاتیکی به میزان ١١٠٠ کیلوگرم به آن وارد شود و بلافاصله پس از انجام این آزمون فاصله بین سطح پایه پنجه فولادی و داخلی ترین تورفتگی لبه عقبی قوس پنجه اندازه گیری می شود که این فاصله نباید از ٣٢ میلیمتر کمتر باشد بعلاوه هیچگونه شکستگی و یا ترک نباید رخ دهد.
- آزمون ضربه : در این آزمایش با استفاده از دستگاه آزمون ضربه یک وزنه ٢٣ کیلوگرمی با سطح برخورداری نیم دایره شکل به طول محوری ٢٥ میلیمتر و شعاع ٢٥ میلیمتر به طور آزاد و در مسیر هدایت شده از ارتفاع ٤٦ میلیمتری روی پنجه فولادی رها می گردد فاصله آنی ایجاد شده توسط برخورد بین سطح پایه پنجه و داخلی ترین تغییر شکل لبه عقبی قوس پنجه نباید کمتر از ٢٢ میلیمتر باشد و هیچ شکستگی و ترک نیز نباید رخ دهد.
لازم به ذکر است آزمون های معرفی شده فوق مربوط به کفش های ایمنی از نوع ضربه گیر می باشند.
- مقایسه روش تولید معمول کشورمان با دیگر کشورهای جهان
روش های تولید در صنعت کفش بر اساس دو معیار اصلی زیر طبقه بندی می گردد:
-
-
- سیستم کارکشی و روش استفاده از قالب ماهیچه (Lasting System)
-
قالب ماهیچه مورد استفاده در صنایع تولید کفش به سه گروه عمده بشرح ذیل تفکیک می گردد:
-
-
-
- سیستم کارکشی با استفاده از قالب ماهیچه فلزی که معمولا بر روی دستگاه نصب می شود.
- سیستم کارکشی با استفاده از قالب ماهیچه پلاستیکی و یا چوبی که به طور جداگانه و به تعداد مورد نیاز در خطوط کارکشی مورد استفاده قرار می گیرد تفکیک می گردد.
- سیستم کارکشی ترکیبی که در این روش ابتدا با استفاده از قالب ماهیچه پلاستیکی، رویه و کفی بر روی قالب سوار شده و به قالب ماهیچه فلزی بسته شده روی دستگاه انتقال داده می شود.
-
-
لازم به ذکر است که هر کدام از سیستم های کارکشی رویه بر روی قالب در ارتباط با روش های مختلف اتصال زیره به رویه تنوع قابل ملاحظه ای را در روش های ساخت و تولید کفش ایجاد کرده و بنابراین روشهای تولید بر اساس دسته بندی مذکور انجام می گیرد.
نمودار ١‐ سیستم کارکشی با استفاده از قالب ماهیچه پلاستیکی نمودار ٢‐ سیستم کارکشی با استفاده از قالب ماهیچه فلزی نمودار ٣‐ سیستم کارکشی به روش ترکیبی
-
- روش اتصال زیره به رویه که بشرح ذیل می باشد:
-
-
- تزریق مستقیم زیره به رویه
- پرس زیره به رویه
- پرس زیره به رویه و دوردوزی زیره
- دوخت زیره به رویه با مغزدوزی
- دوخت مستقیم زیره به رویه
- پرس و پخت زیره
-
در صورتی که این روش تولید با روش های تولید مورد استفاده در سایر کشورها مورد مقایسه قرار گیرد نتیجه گیری میشود که اصول اولیه در سایر کشورها با روش اشاره شده تفاوت چندانی ندارد ولی آنچه که باعث تمایز روش تولید داخل نسبت به مشابه خارجی میشود تمام اتوماتیک بودن کلیه بخش های تولید می باشد به نحوی که کلیه مراحل از طراحی توسط کامپیوتر و ارتباط آن با ماشین آلات و دستگاه های تولید جهت اعمال تنظیمات لازمه بر روی کفش و کنترل های کیفیتی انجام شده در هر مرحله توسط چشم های الکترونیکی متصل به کامپیوتر نشان از تکنولوژی پیشرفته در تولید می باشد.
ماشین آلات مورد نیاز تولید کفش ایمنی
کلیه ماشین آلات تولید کفش ایمنی ساخت داخلی اند و در کشور قابل تهیه می باشد.
ردیف | ماشین آلات لازم | مشخصات |
۱ | ماشین تزریق پلی اورتان (PU) | مخصوص تزریق زیره دو رنگ |
۲ | دستگاه لویس | مجهز به سیستم کلاج‐ ٤ کیلووات |
۳ | گرم خانه | – |
۴ | چیلر | – |
۵ | دورگیر | – |
۶ | میکسر | – |
۷ | چرخ دوخت | تک سوزنه‐دوسوزنه‐ درشت دوز از شماره ٢ الی ٩ |
۸ | دستگاه پرس چرم | ٢٥ تن‐ ٣ کیلووات |
۹ | کمپرسور هوای فشرده | ٥٠٠ لیتر در دقیقه – ٣ کیلووات |
تعیین نقاط قوت و ضعف تکنولوژی مرسوم در تولید کفش کار
نقاط قوت | نقاط ضعف |
١‐ وجود دانش فنی کافی در کشور
٢‐ دسترسی به نیروی کار ٣‐ امکان صادرات به سایر کشورها |
١‐ نوسانات قیمت مواد اولیه ٢‐ پایین بودن سطح فن آوری٣‐ عدم مطابقت کیفیت محصول تولیدی با استانداردهای سایر کشورها٤‐ عدم دسترسی به اطلاعات بازارها |
مواد اولیه عمده مورد نیاز و محل تامین آن
ردیف | ماده | مشخصات |
۱ | پنجه | مقاوم در برابر حداقل٢٠٠ ژول انرژی و فشردگی ١٥ کیلو نیوتن |
۲ | قالب کفش | از جنس پلی اتیلن |
۳ | چرم گاوی سبک | ضخامت ٢ تا ٢,٤ میلیمتر |
۴ | چرم آستری | ضخامت حداقل ١ میلیمتر |
۵ | مواد pu | جهت تزریق زیره |
۶ | پاشنه | pvc |
عمده مواد اولیه این طرح چرم که قابل تهیه از بازار داخلی کشور می باشد. از جمله تولیدکنندگان بزرگ چرم درکشور چرمشهر در واقع در جاده قم ‐ تهران می باشد.
بررسی تاثیرات زیست محیطی
مواد اولیه مورد استفاده در صنایع کفش شامل چرم ها، مواد PVC ,PU، الیاف طبیعی و مصنوعی و حلال ها می باشند. ماده خام چرم از زواید محصولات گوشتی بدست می آید که برای محیط زیست زیان آور نمی باشداما در تبدیل آن به چرم و در طی عملیات دباغی برخی از مواد شیمیایی به آن وارد می شودکه باید به شدت مورد کنترل قرار گیرد. در سنوات اخیر چرم هایی با عنوان چرم های زیست محیطی به بازار عرضه شده است که در این چرم ها به جای کروم از ترکیبات گیاهی برای دباغی استفاده می شود. پلیمرهای PVC , PU و کائوچوی مصنوعی عموما همگی از منابع غیر قابل تجدید مشتق می شوند و در تولید آنها از مواد خطرناک جهت محیط زیست استفاده می شود.
در این مورد موادی که ترموپلاستیک هستند قابل بازیافت می باشند اما در مواردی که ترموست می باشند هنوز جایگزین مناسبی جهت آنها بکار گرفته نشده است. در ساخت پی یو می توان از پلی اول هایی با پایه روغن های ماهیان و آبزیان استفاده نمود. پیوندهای عرضی موجود در کائوچو بازیافت آن را دچار مشکل می کند. چسب مورد استفاده در تولید کفش ها پایه حلال اثرات زیست محیطی بیشتری نسبت به چسب های با پایه آب و چسب های جامد دارد که با جایگزینی این نوع چسب ها از میزان آلودگی در محیط زیست کاسته می شود. مواد مورد استفاده در آستر و روکش کفش نیز می تواند با تغییر یافتن بر مبنای آبی می تواند منجر به کاهش اثرات زیست محیطی تولید کفش شود.
در تولید الیاف مصنوعی مورد استفاده در تولید کفش از مواد شیمیایی بسیار پر ضرر جهت محیط زیست استفاده می شود که امروزه در استفاده از الیاف طبیعی به جای الیاف مصنوعی تلاش هایی انجام شده است. از راه های کنترل ورود مواد اولیه مورد استفاده در تولید کفش به محیط زیست استفاده مجدد از فاضلاب و فضولات سیستم وحداکثر استفاده از مواد اولیه می باشد.
منبع : mistersafetyshoes